一、前言
高端装备关键零部件,如航空发动机热端部件、超超临界汽轮机转子及叶片、铁路轨道、冶金装备等,由于服役环境恶劣,易发生结构、表面损伤而导致高端装备停机或报废。若运用全生命周期制造的思路,通过快速再制造或现场再制造,可延长易损件的服役时间,实现资源的再利用,促进可持续发展。《中国制造 2025》中明确指出:全面推行绿色制造,大力发展再制造产业,实施高端再制造、智能再制造、在役再制造,推进产品认定,促进再制造产业持续健康发展。
激光再制造技术以高功率激光束为热源,运用非接触光加工的方式,可为零件修复与再制造提供新的解决方案,是绿色再制造的重要支撑技术。该技术可快速恢复产品或零部件尺寸,并在性能上达到甚至超越新品,具有修复精度高、工件损伤小、修复区结合强度高、材料利用率高等优点。面向不同领域关键零部件的修复需求,国内外学者主要针对铁基 、钛基 、钴基、镍基合金材料的激光熔覆开展了理论和实验研究,并在航空发动机叶片、汽轮机转子、冶金装备、煤矿机械、高压油泵凸轮轴等领域开展了激光再制造技术的应用基础研究。但激光再制造技术目前仅在少数领域实现了工业应用,面向规模应用仍存在一定的技术与市场瓶颈。
针对激光再制造技术与产业,本文在分析其发展现状的基础上,梳理当前面临的技术问题与应用挑战,并研判发展趋势,提出促进我国激光再制造技术与产业发展的对策建议。
二、激光再制造技术宏观需求分析
(一)激光再制造技术是制造技术创新的前沿领域
激光再制造技术可用于激光再制造的前处理、成形修复和后处理环节,具体分类如图 1 所示。其中,核心环节是激光成形修复技术,如采用激光熔覆成形、激光快速成形以及激光焊接工艺来修复零件缺损部位。此外,激光切割和激光清洗技术可用于零件的拆解和前处理环节,激光冲击强化和激光抛光可用于零件修复件的后处理环节。
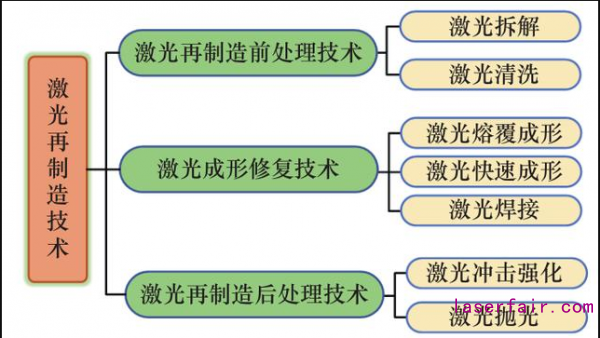
图 1 激光再制造技术分类
基于激光熔覆成形和激光快速成形的激光增材再制造技术,具有能运用稳定的熔池形成冶金结合、界面结合强度远高于镀膜和喷涂以及热输入量小于电弧堆焊的优势,可满足高强度零部件的再制造需求,是先进制造技术的重要前沿发展方向。针对部分大型装备、关键零部件的严苛修复需求,特种修复工艺、多能场激光再制造技术成为当前研究热点。
(二)激光再制造产业是促进制造业转型升级的新兴产业
激光再制造技术在高端装备再制造中占据优势,被认为是制造业转型升级的新一代战略性支撑技术。由激光再制造技术发展而形成的激光再制造产业,为制造业转型升级提供了发展动力。
激光再制造产业在欧美等发达国家或地区已成为具有显著经济和社会效益的产业,极大地推动了制造业的转型升级。为推动激光再制造产业的发展,世界主要国家或地区先后制定了一系列战略建议与政策支持(见表 1)。当前,我国已跻身为制造业大国,但相较于发达国家或地区,生产制造技术的精细化程度仍有待提高。另外,在节能减排的发展要求下,我国也逐渐关注激光再制造产业领域,并推出了一系列战略与政策进行配套支持发展。近年来,我国激光修复与再制造技术在航空、航天、矿山机械、轮机装备、冶金装备等领域初步形成产业,在煤矿液压支架、冶金轧辊、汽轮机转子等动力设备再制造上得到了广泛应用。激光再制造产业成为推动制造业转型升级的新兴产业。
表 1 世界主要国家或地区激光再制造技术及产业相关战略与政策
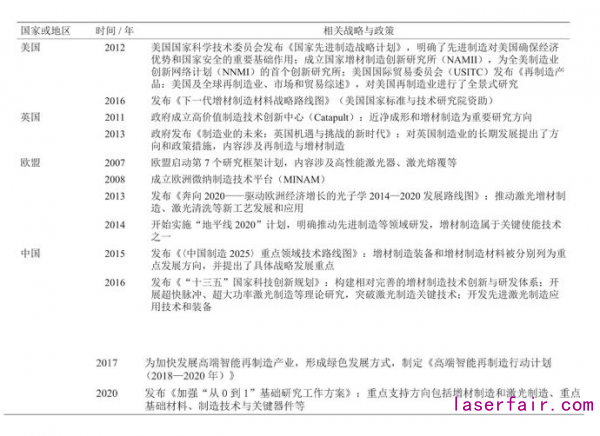
(三)激光再制造产业是促进可持续发展的重要力量
《中国制造 2025》将绿色制造作为五大工程之一,更明确指出要组织实施传统制造业能效提升、清洁生产、节水治污、循环利用等专项技术并加以改造。而激光再制造产业与绿色制造的理念高度契合,为传统制造业可持续发展提供重要支撑。
激光再制造技术具有热量输入集中、工件损伤小、加工速度快等特点,是一种新兴的绿色再制造技术。激光再制造技术可实现关键零部件的快速修复并减少资源浪费,降低停机造成的能源和经济损失,促进可持续发展。另外,激光再制造产业在制造过程中“三废”排放少,污染源可控,这与我国构建循环经济高度契合,并有利于促进节能减排战略需求的部署实施。
(四)激光再制造技术深刻改变着高端装备的设计与运行方式
高端装备制造业的绿色、低能耗、高品质发展已是当务之急,对关键零部件进行全生命周期管理已成为高端装备发展的重要趋势。激光再制造技术的出现和使用,完善了关键零部件全生命周期管理的内涵。具体来说,关键零部件在设计阶段要考虑修复可能性,在服役阶段要考虑使用寿命等的信息反馈,在报废阶段要考虑非破坏性分解等报废方式。同时,通过加强对产品失效分析及剩余寿命变化规律的探索,可以实现零部件失效部位高性能表面涂层的设计与制备以及薄弱部位的加工完善和质量控制。
全生命周期的制造模式将从源头上有效治理制造业污染,弥补设备运行停顿带来的损失,颠覆传统的制造模式。而激光修复与再制造技术作为其中的关键一环,深刻改变着制造业装备的设计思路和运行方式。
三、激光再制造技术发展现状
(一)激光再制造技术在不同工业领域零部件修复中实现应用
随着大功率激光器及其配套设备的不断发展,越来越多的国家加强对激光再制造技术在机械零件制造和修复领域的理论与技术研究。如图 2 所示,目前激光再制造技术已在航空、航天、国防工业、矿山机械、能源动力、冶金装备等工业领域实际应用。国外激光再制造技术的应用主要集中于国防工业及航空、航天领域,如应用激光再制造技术修复航空发动机失效零部件。
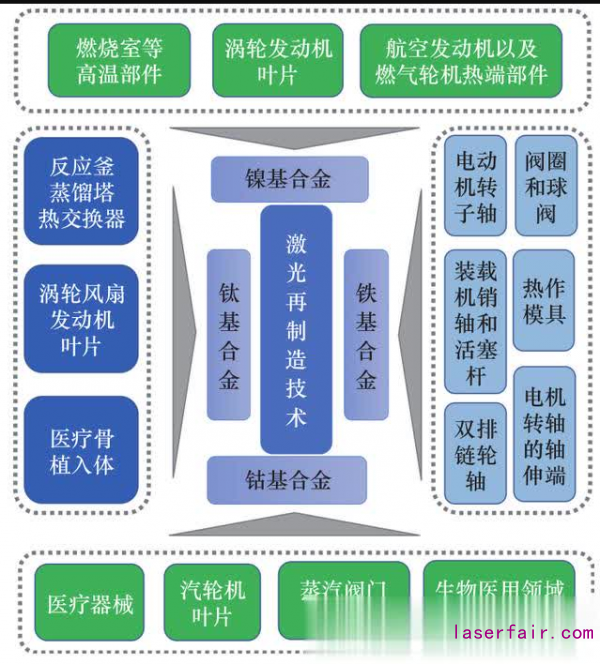
图 2 面向不同工业领域的激光再制造技术
我国激光再制造技术在军用领域主要用于构建军用航空发动机关键零部件再制造核心技术体系;在民用工业领域,激光再制造技术已在矿山机械、能源动力、冶金装备等领域的煤矿液压支架、汽轮机转子及叶片、冶金辊道、芯棒、轧机牌坊等大型装备及关键零部件的修复中实现应用,其中,煤矿液压支架的激光再制造技术已实现了批量化应用。
(二)能场辅助激光再制造成为高质量再制造的重要手段
面向高端装备关键零部件的高质量修复、现场修复需求,单一能束的激光金属成形技术存在易产生气孔、残余应力、微裂纹等缺陷,从而影响到修复件的性能和稳定性。因而,仅仅通过改变激光工艺已难以满足高端装备对精确性、复杂性和高性能等的再制造需求。
据此,国内外学者提出采用电磁场 、感应热场、超声振动等外加能场耦合作用于激光再制造过程(见图 3)。具体来看,面向窄深缺陷修复问题以及严格无气孔要求,引入电磁场调节熔池流动、抑制气孔;面向对微观组织有严格要求的部件,引入超声能场对组织形貌进行调控;面向易开裂材料或部位,引入热场降低温度梯度,降低残余应力风险。当前,能场辅助激光再制造技术已成为研究热点,但相关技术仍处于实验室研发及原型样机研发阶段。面向工业应用需求,亟需在复合制造工艺定型、能场复合集成设备等方面继续开展研发,以满足未来高端装备对高质量、高效率的修复需求。
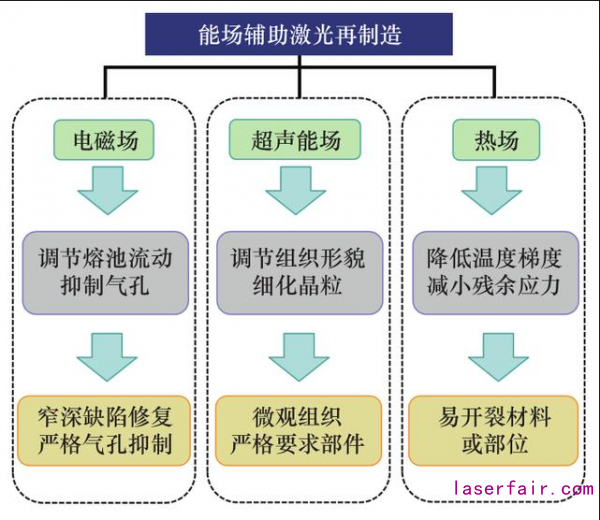
图 3 外加能场在激光再制造中的作用机制
(三)现场再制造是激光再制造技术的重要发展方向
面对尺寸庞大、难以运输的大型设备或大型零部件的修复需求,应用激光现场再制造技术的突出优势可快速实现损伤设备的恢复运行。为便于进行现场再制造,激光设备需小型化、集成化且方便运输,以适应复杂的现场环境和保持较高的稳定性。
采用激光熔覆再制造技术对大型装备或零部件进行修复时,尤其是非水平基面损伤的激光修复,熔池在重力作用下形状易发生变化,这对多角度激光再制造工艺提出了更高的要求。为此,石世宏研究团队采用光内送粉激光熔覆技术,在不同倾角基面下控制激光熔覆头与基面始终垂直,实现了全角度激光熔覆。姚建华研究团队研究了工作气流及熔覆角度对激光修复转子轴质量的影响情况,实现了不同倾角条件下的激光修复 。
四、激光再制造技术发展面临的挑战
以激光再制造技术为代表的装备修复与再制造产业是装备制造业的衍生产业。我国激光再制造技术虽已在矿山机械、能源动力、冶金装备等领域率先得到了应用,但随着高端装备产业的发展对激光再制造技术和产业提出了更多新的要求,如以航空发动机与燃气轮机为代表的高端装备激光再制造技术。目前,我国激光再制造产业与制造业的产业规模不匹配,产业发展存在“小、散、弱”、应用领域少等问题,缺少规模大、技术实力强的国际龙头企业。我国激光再制造技术的应用和发展面临如下挑战。
(一)激光再制造专用材料发展落后
我国激光再制造专用材料“卡脖子”问题突出,具体表现为激光再制造粉材与丝材等专用新材料方面发展较为滞后,专有材料选择局限性较大,面临品种少、供应商少、高性能修复材料缺乏等问题,且专有材料的可靠性、稳定性普遍不高并缺乏验证。目前国外企业面向激光增材制造技术已开发出系列专用材料,如德国斯棱曼激光公司(SLM Solutions)已开发出铝基、镍基、钛基、钴基、铁基、铜基等系列激光增材制造材料,并与自产装备配套建立了稳定的工艺体系。国外的设备厂商在出口时通常采用“装备 + 粉末”的捆绑销售政策,使得我国在进口专用材料时价格昂贵,提高了产品成本,降低了在激光增材再制造领域的竞争力。
(二)核心装备及部件依赖进口
我国在激光再制造领域已具备一定的装备研发能力,但仍以面向工业应用的设备集成开发为主,其核心器件,如高光束质量激光器及光束整形系统、高品质电子枪及高速扫描系统、大功率激光扫描振镜、动态聚焦镜、阵列式高精度喷嘴 / 喷头等精密元器件仍然严重依赖进口,国产激光制造装备在工艺稳定性、环境温度控制等方面与进口品牌仍有较大差距。我国目前已有大族激光智能装备集团、华工激光工程有限责任公司等一批具有国际影响力的设备厂家,但高端激光装备市场仍以国外先进企业为主导,如通快集团(Trumpf)、阿帕奇公司(IPG)、美国相干激光公司(Coherent)、利泽莱恩激光公司(Laserline)等。
(三)企业对激光再制造技术的理解和认识不足
激光再制造技术为高端装备修复与再制造提供了新的解决方案,但该技术尚未被装备行业广泛接受和认可。具体原因有:一方面,部分传统装备企业对于新技术的敏感度较低,需要加强推广提高认识;另一方面,在某一装备领域引入激光再制造技术时,需经过严谨的科学分析与完备的工艺验证,盲目引入新技术将带来装备运行风险。另外,在产品全生命周期管理中,产品和材料设计需考虑零部件的维护保养与再制造,而传统装备部件在设计时并未考虑采用激光再制造进行部件维修,因此,部分装备部件受结构形式或材料选型方面的限制难以应用激光再制造技术。
(四)行业标准及体系不健全
在激光修复与再制造领域,我国已有《激光修复技术 术语和定义》、《激光修复通用技术规范》等国家标准以及部分机械行业标准和企业标准,但尚未建立完整的激光再制造技术标准体系,这制约了相关技术成果的累积、固化、推广和应用。由于欠缺统一的行业标准体系,部分企业在激光修复过程中对材料选型和工艺的科学考虑不足,导致修复件失效,造成财产损失甚至是安全事故,进而给激光再制造技术的行业推广带来了负面影响。
五、激光再制造技术的发展目标
近年来随着激光修复与再制造技术的不断发展,我国激光再制造产业已初具规模。经估算,2019 年我国激光修复与再制造产业规模约达到20 亿元,激光再制造技术在工业修复领域已经展现出巨大的应用潜力。未来随着修复质量、效率、智能化等方面的进一步提升,激光再制造技术将进一步得到推广和应用,对装备设计理念、产业结构、制造服务产生深远影响。考虑到技术、产业、理念的革新,激光再制造技术今后分阶段的发展目标如下。
(一)面向 2025 年的发展目标
对接《中国制造 2025》提出的再制造发展战略,针对高端装备关键零部件对提高修复质量和效率的迫切需求,解决目前激光再制造产业“小、散、弱”的现状,到 2025 年,激光再制造技术和产业的发展目标为:全面提高激光再制造装备、材料、工艺水平,不断满足不同工业领域关键零部件对高质量再制造、现场再制造、在役再制造技术的需求;提高激光再制造及其前后处理工艺的综合效率,满足高效再制造的需求;对接“两机”国产化战略,解决“两机”热端部件等核心部件修复需求;以规模化为发展目标,在技术发展和成本下降的基础上扩大应用领域、扩大产业规模。预计到 2025 年,我国整体激光再制造产业规模将达到 100 亿元。
面向 2025 年的重点发展方向为:在技术层面重点发展激光复合再制造及其关键装备、高速 / 超高速 / 宽带激光再制造装备与工艺、复杂形状热端部件高质量激光增材再制造技术、激光再制造过程中的同步检测与控制、恶劣现场环境下的激光再制造技术;形成激光复合装备制造业、修复服务业、修复专用粉材及丝材产业;激光再制造技术向多个领域及其零部件延伸,形成规模化的现场激光再制造服务行业。
(二)面向 2035 年的发展目标
制造业服务化已成为制造业转型升级的主要方向,而激光再制造技术是回收再制造服务的重要支撑技术。为了支撑分布式的激光再制造服务体系,到 2035 年,激光再制造技术和产业的发展目标为:智能化激光再制造技术趋于成熟,零部件激光修复实现自动便捷操作;激光修复与再制造技术形成标准化体系;面向不同工业领域对激光智能修复技术的需求,形成成熟的激光再制造产业链。预计到2035 年,我国激光再制造产业规模达到 500 亿元。
面向 2035 年的重点发展方向为:在技术层面重点发展缺陷自动识别与修复工艺智能规范技术、激光智能修复与再制造技术、激光再制造件寿命精确预测技术;形成激光再制造专用装备、智能化控制系统及软件、修复专用材料、再制造服务四大产业。
(三)面向 2050 年的发展目标
人与自然和谐发展是人类文明发展的必由之路,随着再生产品和循环经济理念的深入人心,再制造技术将走向普及化、家用化。到 2050 年,激光再制造技术和产业的发展目标为:小型化激光快速修复装备与配套工艺技术成熟;实现极端条件和环境下的激光再制造;以激光再制造为核心技术的制造服务在高端装备业普及化。
面向 2050 年的重点发展方向为:在技术层面重点发展细小损伤的精确监测以及微观组织层面的精密修复;深海、太空、两极等极端环境下激光再制造;高端装备销售业转型为高端装备服务业并成为主流;激光再制造技术支撑再生产品和循环经济的普及。
六、激光再制造技术发展建议
(一)加强战略层面的积极引导
建议加大对激光再制造专用材料、核心装备及部件等重点领域的财政支持力度。充分利用国家重大专项、国家重点研发计划等资金渠道,采用高校、科研院所、企业、用户相结合的方式,在不断推动通用型设备及工艺发展的基础上,重点支持面向典型易损件的专用激光再制造装备、材料及工艺的研发。
(二)建立激光增材再制造材料基因组体系
激光增材再制造技术的不断发展对专用材料提出了更高的发展要求。由于专用材料的非平衡亚稳态特性,与传统材料相比,专用材料的设计与研发难度更大、周期更长、过程也更复杂,传统的方法已难以满足现在的发展需要。因此,建议尽快建立具有自身特点的激光增材再制造材料基因组体系,提高专用材料的非平衡亚稳态特性,并建立具有自身基因组高通量的计算依据及理论。
(三)加快建立完善标准化体系和高层次应用型人才培养体系
建议提高对激光再制造技术及产品的研发、检验与认证的能力,努力促进标准化与产业紧密结合,建立完善的激光再制造产业发展标准体系。加强国际合作,积极对接国际标准化组织,开展相关标准的建立、转化及完善工作。同时,聚焦我国在激光再制造领域专门人才和行业规范欠缺的情况,依托国家现有人才培养与引进政策,不断完善高层次应用型人才的培养体系建设。
(四)加大应用推广力度,引导行业整合
建议将政府支持与各种行业资源相结合,加强我国激光再制造产业各分领域的联系,拓宽产业与政府、产业链上下游、产业之间以及生产企业和用户之间的对接通道,加快技术的推广应用。着重开展分层级、分领域的试点示范专项行动,点面结合,协同推进,积极引导和促进社会力量及地方政府的投入,共同推进激光再制造技术的深度应用,促进我国激光再制造产业的持续快速发展。
(五)加强“产学研用”协同创新,加快关键共性技术创新发展
建议在激光再制造、全生命周期制造等领域建立国家级研发平台,由高校、科研院所和骨干企业牵头,打通产业链的上下游,形成完整的材料、装备、工艺、检测、应用体系,加快对关键共性技术的攻关和创新发展。面向不同行业领域,设立各具特色的再制造产业联盟、再制造产品评估与检测中心以及协同创新中心等。