德国LIMO公司是世界知名的大功率半导体激光器的供应商,凭借其领先的半导体激光应用技术,与众多工业界客户建立广泛的合作,并为其提供先进的激光应用解决方案。LIMO已经为众多先进制造企业(包括西门子、大众汽车等)提供过半导体激光塑料焊接机系统、半导体激光金属熔敷机系统、半导体激光材料处理机系统、半导体激光切割机系统、半导体激光医疗机系统等等。
德国LIMO公司激光焊接系统具有如下特点:
特点一:快速而经济的半导体激光塑料焊接系统
1)LIMO的应用实验室为您提供工艺参数优化。
2)激光工艺头可根据工件的几何形状精确可调,利用微光学组件实现同步快速的焊接工艺。
3)使用非接触工艺,即使复杂的3D表面也能很容易实现,而不需要复杂的机构。
4)相比传统的焊接技术,具有最高亮度和优异的功率稳定性的半导体激光器可以确保快速的加工工艺和良好的重复性。
特点二:完美的焊接外观
1)高性能无缝焊接
2)无渗水、无气泡焊缝
3)焊缝宽度恒定
4)所有的颜色均可焊接
应用举例:
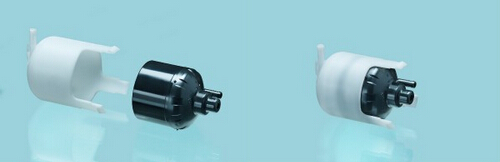
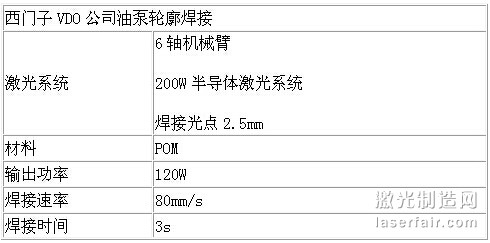
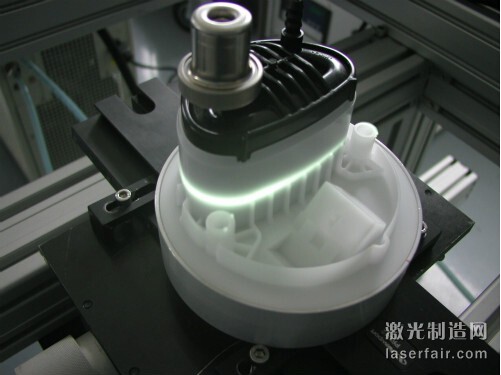
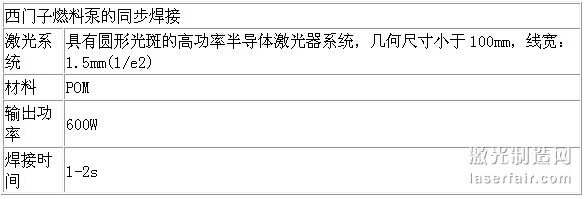
特点三:安全的焊接
1)密封焊接(符合DVS22262-4准则)
2)很小的热效应区域
3)非破坏性焊接工艺
4)在高速下焊接几乎不变形
5)非接触式工艺
特点四:清洁的焊接
1)无粘合剂的焊接工艺
2)无化学反应的焊接
3)清洁卫生,被允许用于医疗卫生包装
4)无颗粒的焊接
应用举例:
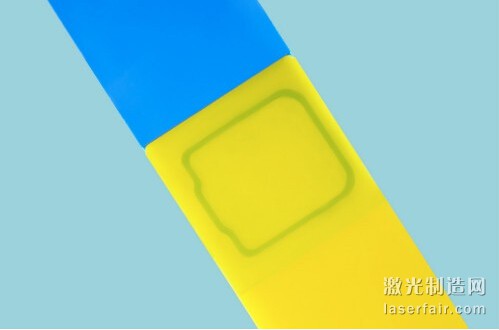
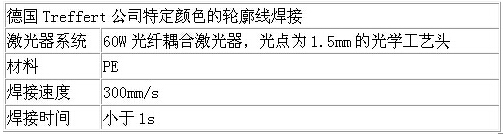
特点五:焊接可靠
1)焊缝拉力满足DVS22032-5标准(拉力测试2203-2,拉力冲击测试2203-3,拉力蠕变测试2203-4,弯曲测试2203-5)
2)免维护
3)长寿命,其寿命取决于半导体激光器的寿命
4)工艺稳定
5)重复性高
特点六:使用简单
1)LIMO提供工艺参数
2)LIMO提供系统集成和安装服务
3)所有配件均是模块化设计
4)无部件磨损
5)被动式气冷或水冷,无需DI循环水
6)可实现远程控制
7)使用光纤传输激光光束,无需大的使用空间
LIMO的应用中心提供如下工艺:
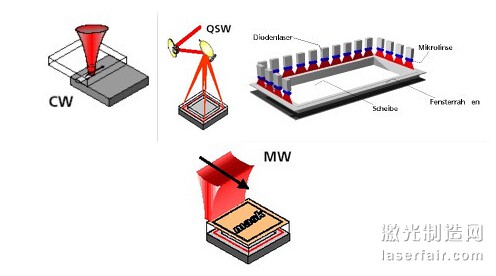
1)轮廓焊接(CW:Contourwelding)
2)准同步焊接(QCW:quasisimultaneouswelding)
3)同步焊接(SW:simultaneouswelding)
4)掩膜焊接(MW:maskwelding)
应用领域:
汽车制造、电子、半导体、医疗医药包装、食品级包装、金属加工、材料表面处理
同时我们欢迎国内广大设备整合商一起合作开发相关激光焊接系统,共同服务于国内外客户。
应用介绍:
德国LIMO激光技术应用于塑料焊接
除了传统的焊接方法以外,用激光焊接塑料已被证明是一种可行的焊接方法。目前,利用激光焊接方案已经能够焊接汽车、电子、医疗设备制造中的敏感零部件,并能服务食品包装和消费电子市场。
半导体激光器加工优势一览:
最小的机械应力
最小的热应力
稳定的焊接过程
极大的焊接灵活性
完全无粒子产生
内部连接
小的熔融物喷射
不需要附加的吸收剂
高质量和牢固的焊接质量
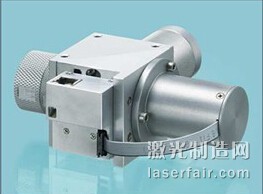
带高温反馈的激光工艺头
实现完美表面与牢固焊接的灵活过程
为了得到具备完美表面的牢固性焊接,通常使用重叠和光束透射焊接(transmissionwelding),对红外区域的激光能量的吸收,通常是用 颜料(如烟灰)实现的。在透射焊接中,激光辐射透过一个被焊接的部件,被另一被焊接的部件吸收。现在,激光能够焊接多种颜色的肃塑料,并通过向焊接处添加 各种颜料实现更高的焊接牢固性。相比于粘接、超声焊接、振动焊接以及热焊接等传统的焊接方式,激光焊接技术拥有诸多优势。
粘接通常需要对接触面进行预处理,并且要使用有机溶剂。热焊接虽然成本较低,但焊接速度相对缓慢,并且容易有磨损发生。而且,通常这种焊机方法的热影响区域较大,因此不适合敏感零部件焊接。
摩擦焊接、振动焊接和超声波焊接,将会对焊机部件施加较大的机械力,这使得焊接结构更为复杂,并且需要定期机械检查。
与上述焊接方法相比,激光焊接的优势凸显。激光焊接产生最小的热应力和机械应力。并且,激光焊接非常清洁,没有颗粒产生,也不需要溶剂,并且具有高度灵活性。焊接是在被连接的物体内部进行的。
焊接过程的可靠性与控制
实际应用表明,在激光焊接应用中,高温计是一个非常有用的工具。高温计与德国LIMO公司的高功率半导体激光器系统相结合,能够实现非接触式温度测量,并且能够快速调节温度,保持稳定。这种闭环控制系统,能使焊接过程始终保持在一个恒定的温度下进行,以避免由于过热所造成的损伤。
温度信号可以在一个定义的过程窗口以图标的形式生动显示出来,这样就能够随时发现焊接不合格的部件,将其挑选出来。除此之外,LIMO还提供具备一个色彩校正f-Theta透镜的检流计扫描镜。
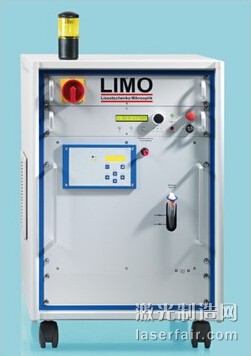
产品
德国LIMO公司的高功率半导体激光系统已形成完整的产品体系,波长覆盖绝大部分塑料焊接所需波长,功率范围覆盖几瓦至千瓦量级,光纤芯径 100um,200um,400um可选。德国LIMO公司高功率半导体激光系统带工业水冷机,电源和控制器于一体,通过24V接口控制,19'标准机箱 外壳包含激光器和冷却系统的设计为OEM集成商提供最简洁的组装模式,具有运行稳定,可靠性高等优点。
定制的配件,如在不同焦距的光学加工元件,均匀光束和扫描仪校长,是选择与测温仪装备,完整的产品系列,使这一制度对基于激光的塑料焊接的理想工具。
(来源:荣格)